March 16, 2023
NAPA and Elomatic: unpacking the secret behind two decades of successful collaboration
Behind every great vessel is a great team – but what makes a great team even better?
Building the blueprint for successful collaboration, data-driven solutions are enabling faster design, better communication and more innovation. When that basis is established, designing safer, greener and more efficient ships becomes significantly easier.
Transforming the industry one project at a time, NAPA and Elomatic have been working together for more than 20 years to create the ships of the future. Helping the team continuously innovate and level up their approach to ship design, we’ve been actively listening, asking the right questions and supporting the team every step of the way.
Reflecting on the last few decades, we recently sat down with Rami Hirsimaki (Senior Vice President, Marine & Offshore), Markus Jokinen (Design Manager, Marine & Offshore) and Elias Penttinen (Consulting Engineer, Marine & Offshore) from Elomatic to unpack their experiences using NAPA and the impact we’ve had on the business in helping their customers tackle the strategic challenges of tomorrow.
Elomatic brings 52 years of heritage as a leading European engineering and consulting company, working across a wide range of projects and vessel types. Currently, their most urgent challenge on the horizon is future-proofing ship designs for the green transition.
Future (fuels) planning
Low and zero-carbon fuels will be critical to shipping’s green transition – but how do they influence ship design?
When it comes to alternative fuels, something especially interesting in ammonia and LNG is the amount of volume they need… so we need a way to quickly explore different options, and NAPA is a very handy option for that.
– Markus Jokinen, Design manager, Marine & Offshore in Elomatic
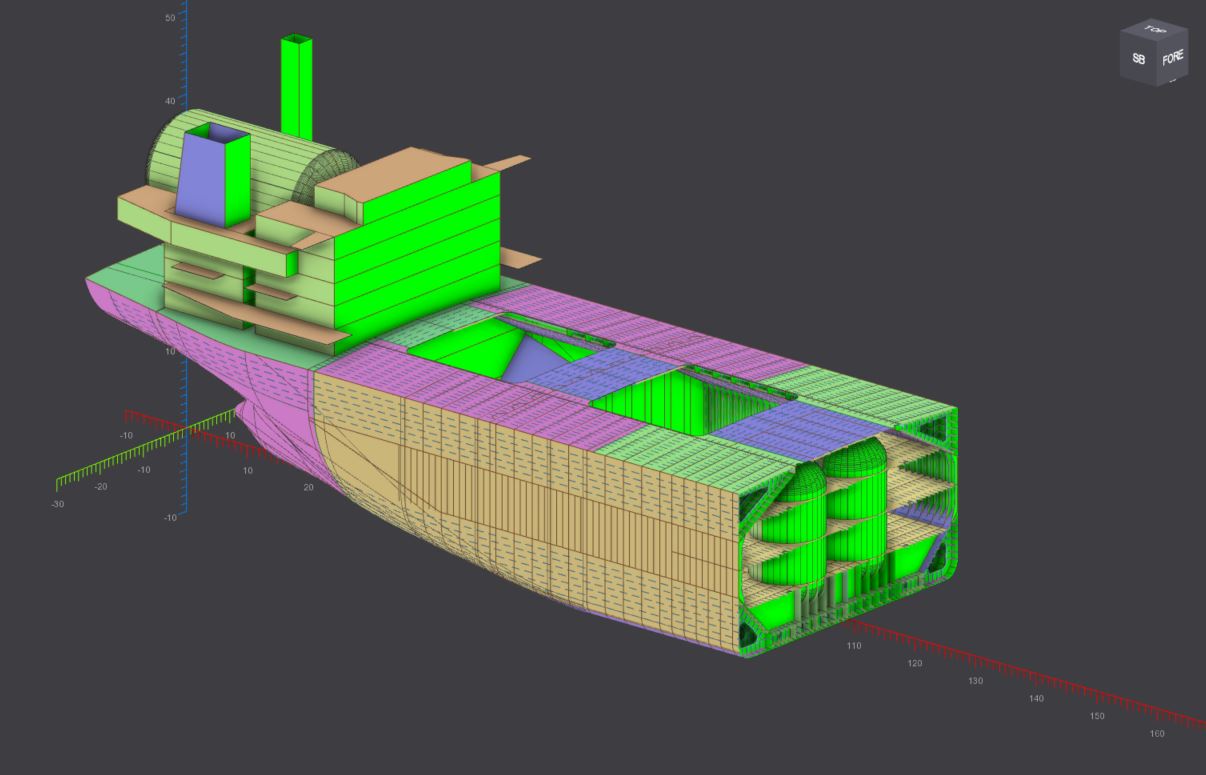
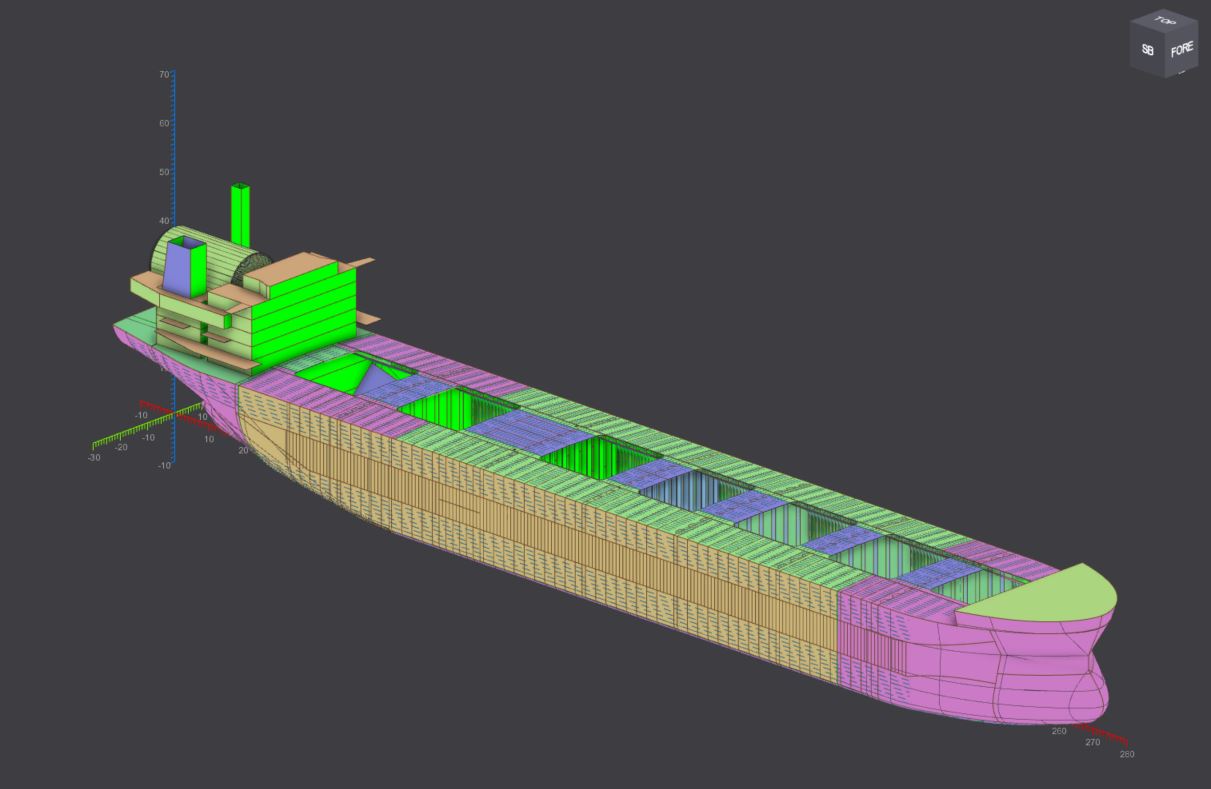
Understanding this problem was essential when Elomatic’s team was tasked with designing a new fleet of ammonia-ready LNG-fuelled vessels for Nippon Yusen Kabushiki Kaisha (NYK), consisting of two bulk carriers (Post-Panamax and Capesize), one (1) Pure Car Carrier (PCC) and one (1) Very Large Crude oil Carrier (VLCC) oil tanker. These vessels needed to be powered by green energy without compromising efficiency or safety.
Carbon-free marine fuels like ammonia will lead the way for the industry’s decarbonization, but to facilitate this transition, NYK, a leading Japanese shipping company, had to consider ways of using LNG as an effective bridge solution to reduce GHG emissions. Vessels that sail using LNG can then easily be converted to an ammonia-fueled vessel at minimal cost, which was a design priority for their team.
Concept design for an ammonia-fuel ready LNG-fueled vessel of Pure Car Carrier (PCC)
Concept design for an ammonia-fuel-ready LNG-fueled vessel (ARLFV) of Very Large Crude oil Carrier (VLCC)
However, given their lower energy density than conventional fuel oil, retrofitting or designing vessels to sail on future fuels comes with its own challenges, such as the need for larger tanks. Traditionally, this almost always involves a trade-off between different design elements. Equally, while adopting new low-carbon fuels creates a myriad of possibilities, it also brings uncertainties and demands a more innovative approach to ship design. Repeating old design methods would no longer be fit for purpose or enable confident decision-making.
Designers and engineers also recognize that safety and efficiency are non-negotiable; so how would stability and operational profiles be affected by design decisions about engine modifications, safety systems, tank size and positioning?
Fortunately, the detailed 3D models for rooms and structures within NAPA Designer allowed Elomatic to address all these concerns and visualize different design options around tank shape, size and layout that would work to help minimize conversion work and cost, without ever compromising on efficiency or safety.
3D models, like NAPA Steel structural models, provide a common software base where drawings, feedback, calculations and analyses all take place – and ensure that any changes are reflected in all outputs. These are complemented by web-based information-sharing platforms that help streamline reviews and approvals. NAPA Viewer, for instance, gives owners, subcontractors and class societies access to all the information they need in real-time, whilst also ensuring that the intellectual property rights of each party are protected.
Model behavior
With increasingly complex design projects, the advantage of using NAPA is that it holds all the necessary data in one place, bringing much-needed clarity to decision-making and transitioning to future fuels. According to Markus, this ‘makes it easier and quicker, especially in the concept phase, to explore these different options.
Should designers allocate lower deck space to make the installation of alternative fuel tanks easier, for example? How would this impact cargo capacity? Given ammonia’s lower energy density? How would tank design influence efficiency?
For Elomatic, it was crucial to confidently answer all these questions and assess the impact of adopting future fuels.
When producing a concept design for NYK’s ammonia-ready Post-Panamax bulkers, Elomatic needed to consider the best design option for safety and efficiency, while minimizing conversion costs. To enable this, we worked closely with their team to optimize the use of 3D structural models on NAPA Steel.
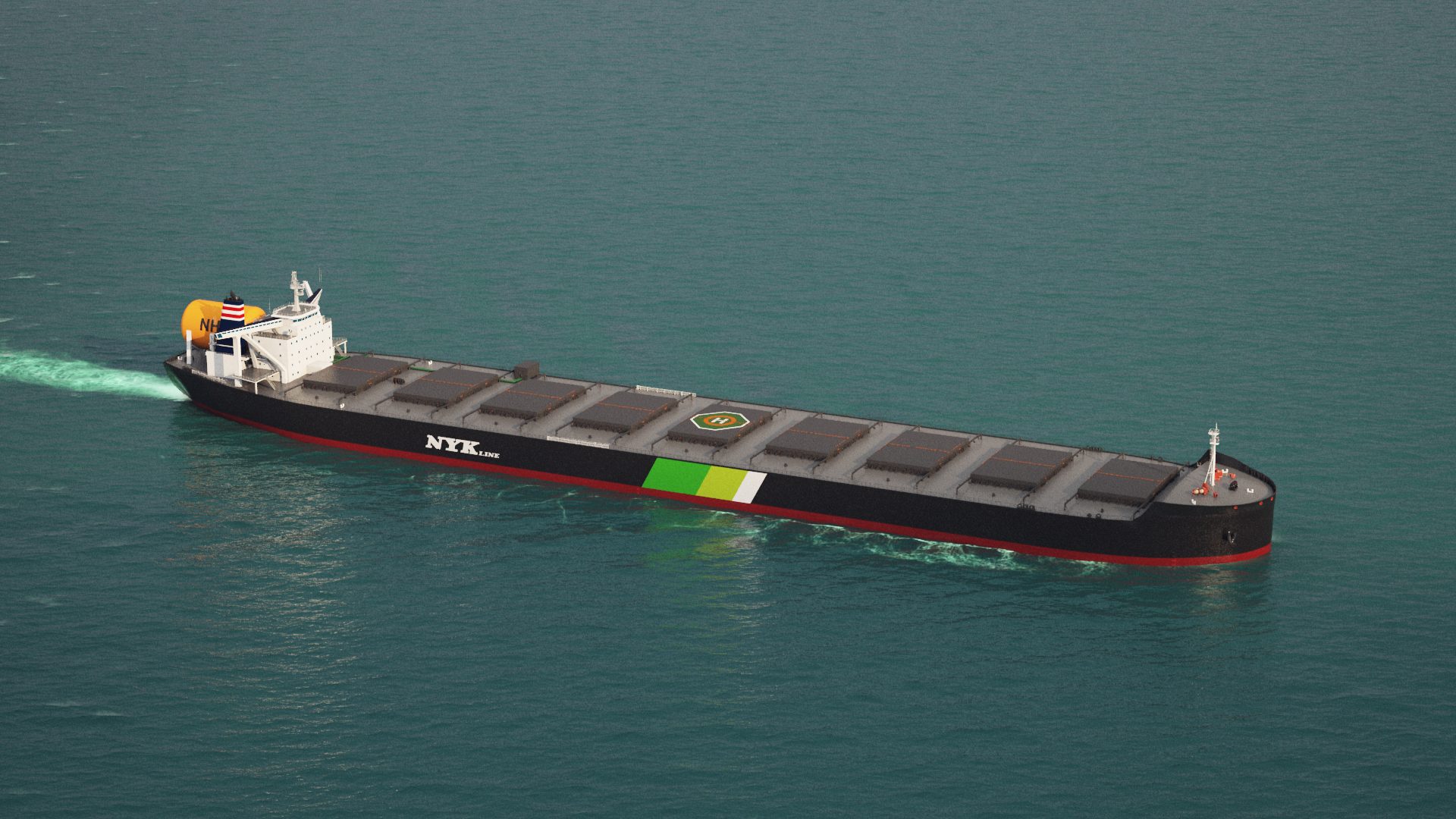
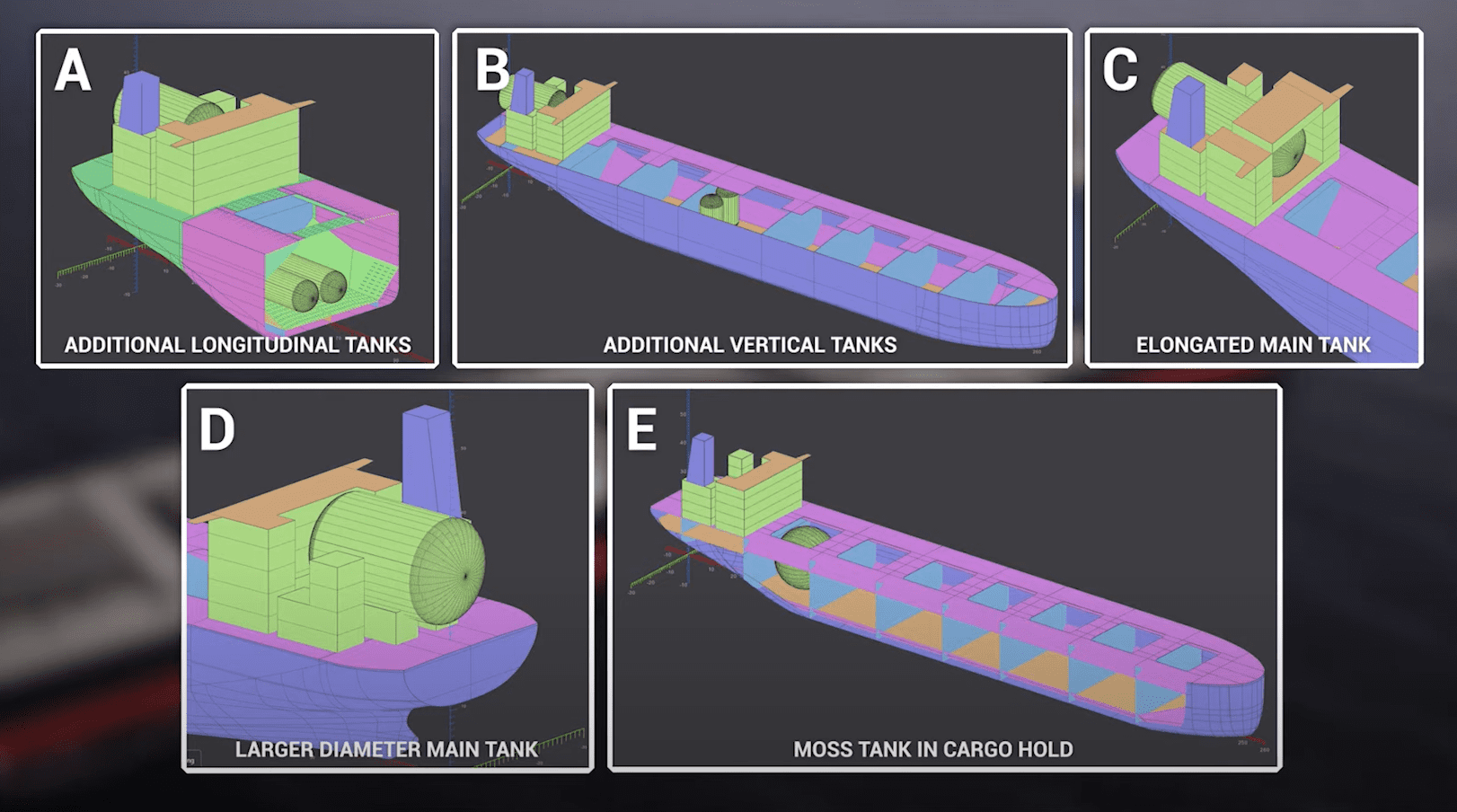
3D models encompass a huge amount of information on a vessel, both at the design and operational stage, that can influence a vessel’s safety and operations. An example is Finite Element (FE) analysis. Often a later consideration, FE analysis forms a crucial part of ship design that identifies the magnitude of stress levels in a model. Using FE analysis at the earliest stages of the structural design enables engineers to understand how new features will work together and impact the integrity of the global structure. With NAPA’s FE meshing solution, Elomatic was able to easily extract and analyze FE models as a standard part of the design process and work out fixes earlier than ever.
A single source of truth
With 3D models serving as one single ‘source of truth’, it’s infinitely easier to make fast design changes and conduct reliable analyses, from hydrostatics, stability, ship weight estimation and hydrodynamics to steel structures and FE analysis. These can even be used for classification approvals.
When producing a concept design for an ammonia-ready LNG-fueled vessel of a Pure Car Carrier, NAPA’s 3D models allowed the team at Elomatic to study how changing tank capacities and positioning would influence a vessel’s stability profile. Further, 3D models made it easier and more precise for the team to fulfill design checks for greater confidence, for example around rule compliance with probabilistic damage rules (SOLAS 2020) by using NAPA’s probabilistic damage stability application, by other NAPA’s hydrostatics and stability modules, and NAPA Steel.
Using NAPA Designer and its 3D graphical interface, Elomatic was able to switch between our earlier text-based interface to the newer graphical one, enjoying the flexibility and insights offered by both versions, especially while studying hydrodynamics, for a more detailed, user-friendly design process.
This ‘single source of truth’ is also fundamentally changing the way teams work by giving stakeholders throughout the process, from naval engineers and architects to tech developers and class societies, access to the same real-time insights to pursue a range of design objectives. For Elomatic, easier communication helped significantly minimize workload and the risk of error, to better meet design timelines, budgets and requirements.
Importantly, NAPA design software is laying the foundations for a more agile and innovative design solution with multiple use cases.
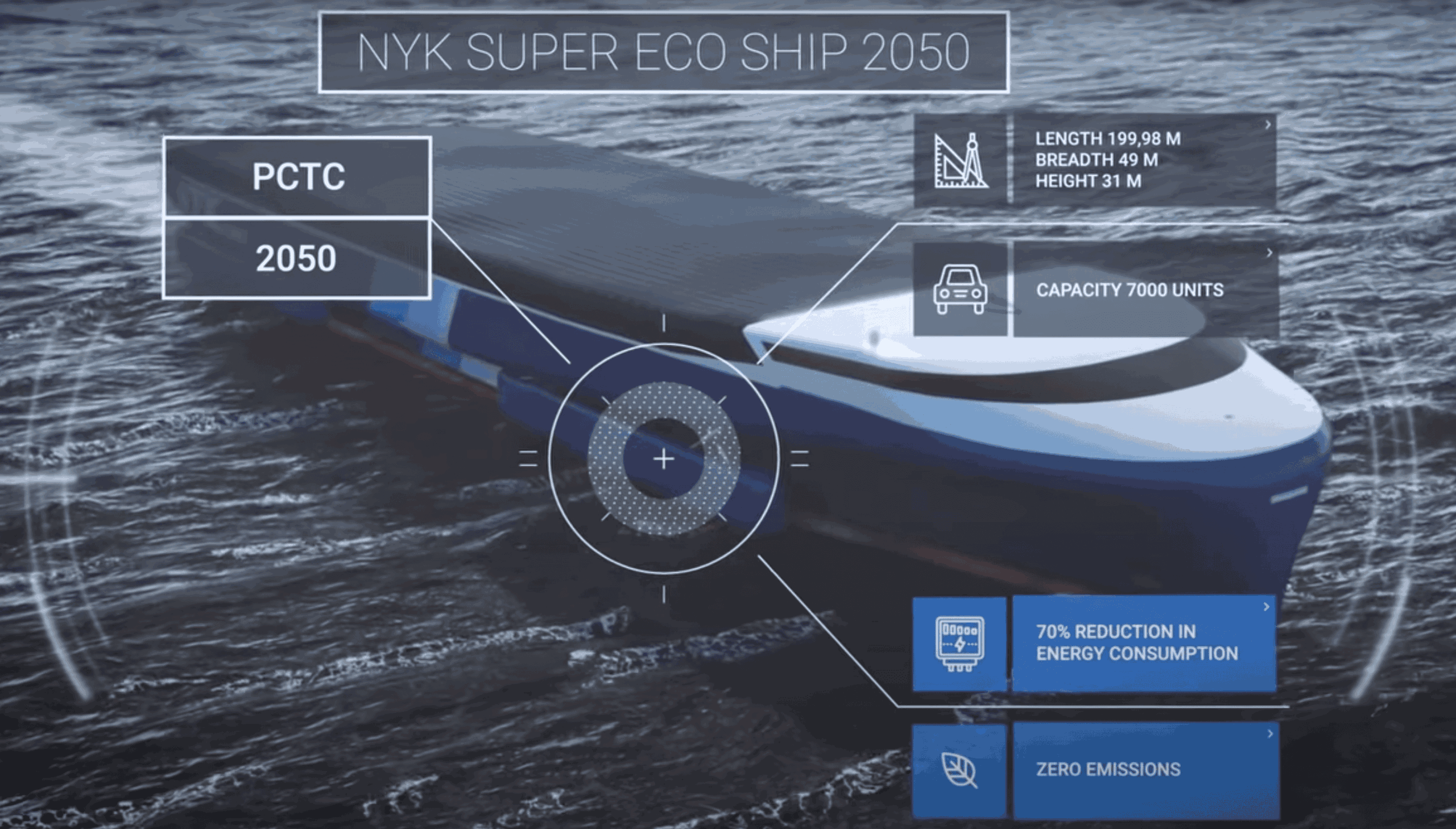
Moving offshore
Our solution doesn’t stop with commercial vessels. Using the same insights on modeling, geometry and stability from NAPA’s design software, Elomatic expanded their presence in the offshore wind power generation market. Given the project’s complexity, Elomatic needed a powerful design solution that could be relied upon for accurate stability calculations.
Supporting the team in meeting its design ambitions, NAPA’s design software was able to reliably and accurately support the design of floating offshore wind structures. With the aim of building a turnkey solution that could easily be installed at sea, NAPA enabled the team to move as quickly and confidently as it would when designing a commercial vessel.
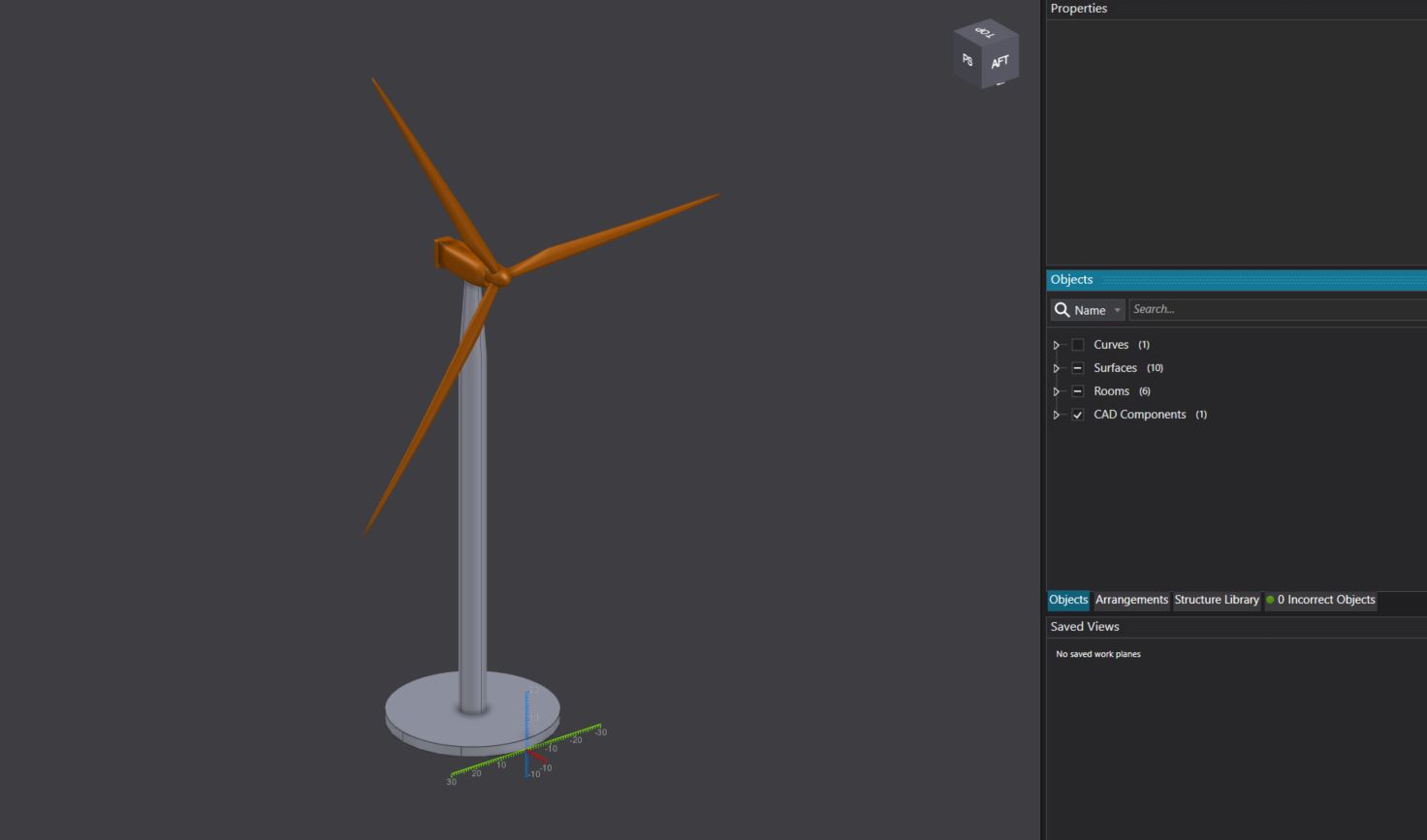
At its core, the aim was to ensure the solution was scalable to break down some of the barriers to the global energy transition.
The dream team
Over the years, regular discussions and close collaboration have enabled NAPA to support Elomatic with its retrofit and newbuildings.
NAPA’s customer service team takes this one step further. They go beyond just troubleshooting design problems- they offer valuable and insightful guidance on how to best use digital tools to achieve ambitious design requirements.
This stems from the recognition that the ships of the future, or even the floating offshore wind structures of tomorrow, will be designed today and need to have sustainability, safety and efficiency integrated into their DNA, every step of the way. How we work together to build more collaborative and innovative processes will determine how we decarbonize the industry and that all begins at the drawing board.
Got interested?
With the NAPA solutions for ship design, you can improve your design process. Contact us to learn more!