KYMA: using 3D models to power yacht design innovation
The world of yacht design is one of constant innovation. Evolving customer demands are continuously prompting naval architects and structural engineers to push the boundaries of creativity, while ensuring safety and a smooth, efficient design process. Here’s how, using NAPA tools, KYMA is harnessing the latest advances in 3D ship design to turn this challenge into an opportunity.
Based in the Italian town of Follonica, on the coast of Tuscany, KYMA is an engineering and consultancy company with more than 20 years of experience developing high-end yachts and other tailor-made leisure vessels. Working with some of the world’s leading shipyards, the expertise of their 40 strong team spans design and structural planning to engineering, on-board systems assessment, and consulting.
Yacht design is a buzzing and fast-evolving sector, explains Nicola Serafini, CEO and Co-Founder of KYMA. The customer requirements are constantly becoming more complex and specific. Meanwhile, we must develop projects to ever-tightening schedules, which adds another level of challenge”, he highlights.
Unique design challenges
KYMA’s high-end yachts are tailor-made, so responding to the customer’s demands and unique expectations is essential. Design challenges may come from new hull shapes or slanted bridges with fewer pillars, for example. There are sometimes helicopter bridges to incorporate. With the latest trends, doors are getting bigger and glass areas wider, creating openings that must be considered in the overall structure. Ensuring the structural integrity and safety of those concepts is vital, and this is where NAPA’s 3D models and design tools play a central role.
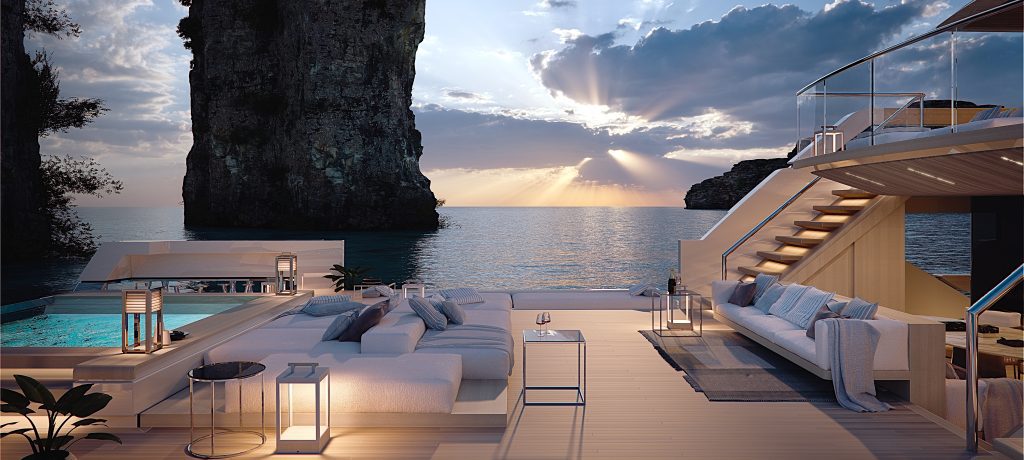
Sanlorenzo Superyacht – 44X-Space designed by KYMA Kyma handled nesting documentation, functional diagrams, 3D engineered model, piping and coordinates, and shipyard support.
“Only with 3D analysis and Finite Elements Meshing (FEM) can we ensure the feasibility of those new shapes”, says Sergio Allegria, CEO and Co-Founder of KYMA. NAPA’s tools enable engineers to incorporate the details of the envisioned components into the ship’s 3D model and transfer it directly to the FEM analysis module. This saves significant time as they no longer need to prepare dedicated 3D models for each FEM analysis.
Crucially, using 3D models allows for quick iterations, enabling engineers to make changes directly in the 3D model and export it swiftly to run FEM analysis as many times as needed. This is critical to be able to test different design variations, which is particularly important for innovative structures. “The more complex these new shapes and features, the more frequent and accurate FEM analysis has to be”, Mr. Allegria highlights.
3D models in action
These gains were particularly evident during the recent design project of an 85-meter yacht, developed by KYMA for a construction site of the Italian Sea Group. KYMA used NAPA Steel, NAPA’s structural design solution, to design the hull and superstructure, and then create the entire steel structure of the ship. This enabled teams to develop the vessel’s 3D model from the early design stages, which served as a “single source of truth” ensuring data consistency and supporting collaboration between all disciplines involved throughout the project.
NAPA allows us to have a single model that we can use in all design phases, which brings everyone on the same page and helps us avoid any misunderstandings throughout the development of the project.
explains Stefano La Cava, Head of Structure Department at KYMA.
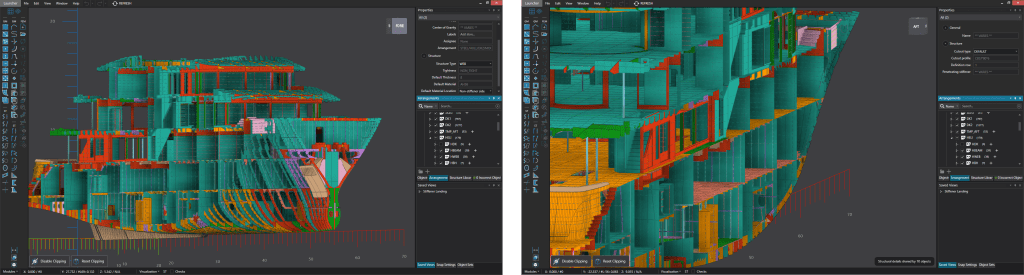
Yacht structural design modeled by KYMA in NAPA Designer
A key advantage of 3D models is that they enable different disciplines to work simultaneously on a project, with up-to-date and consistent information. Once the fundamental structure of the vessel is created in 3D, this provides a baseline which enables KYMA teams to work on the design of systems, fittings and interior furnishings even before the nesting of the first structural blocks is completed.
NAPA allows us to save a lot of time. Now we can make a 3D model of a hull in two months. Before NAPA tools were implemented, we had to build all the different blocks separately, so it could take a year before we had all blocks ready. – Sergio Allegria, CEO and Co-Founder of KYMA
Importantly, the 3D model can be used seamlessly for FEM analysis, and then for downstream production design. “We were able to model the entire yacht for the Italian Sea Group with NAPA, which allowed us to supply the preliminary materials to the construction site. As a result, they were able to order materials early, which helped reduce production times”, Nicola Serafini points out.
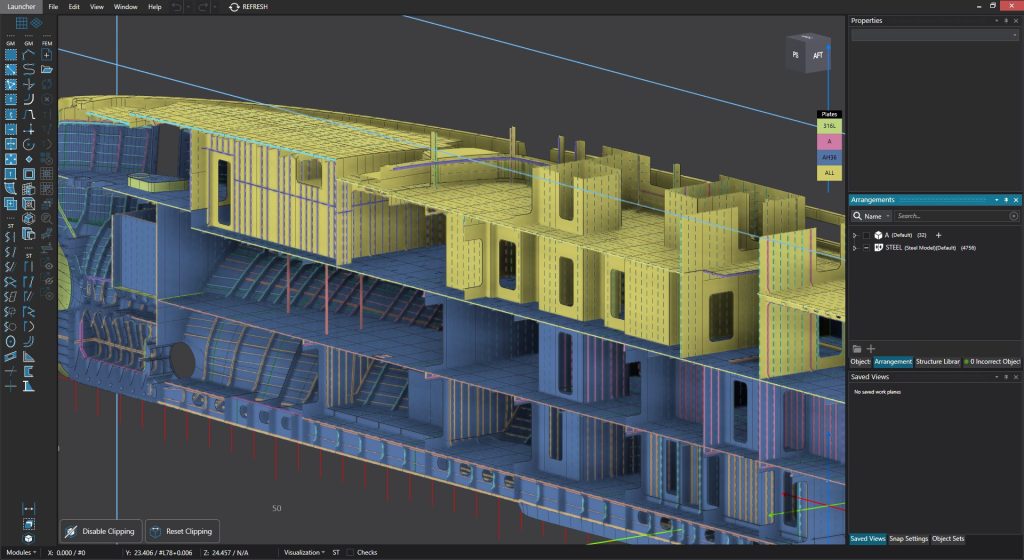
Yacht structural design modeled by KYMA in NAPA Designer
For the design tasks where 2D drawings are still used, NAPA has created a technology environment where 2D and 3D features can coexist in harmony, boosting efficiency even further. “NAPA tools are very important because they allow us to get a 3D and 2D view, depending on the needs. They also provide a critical insight: a preliminary evaluation of the ship’s weight, which enables us to provide a list of materials to the shipyard even at the preliminary design stage”, says Emma Roncaglia, Basic Structural Designer at KYMA.
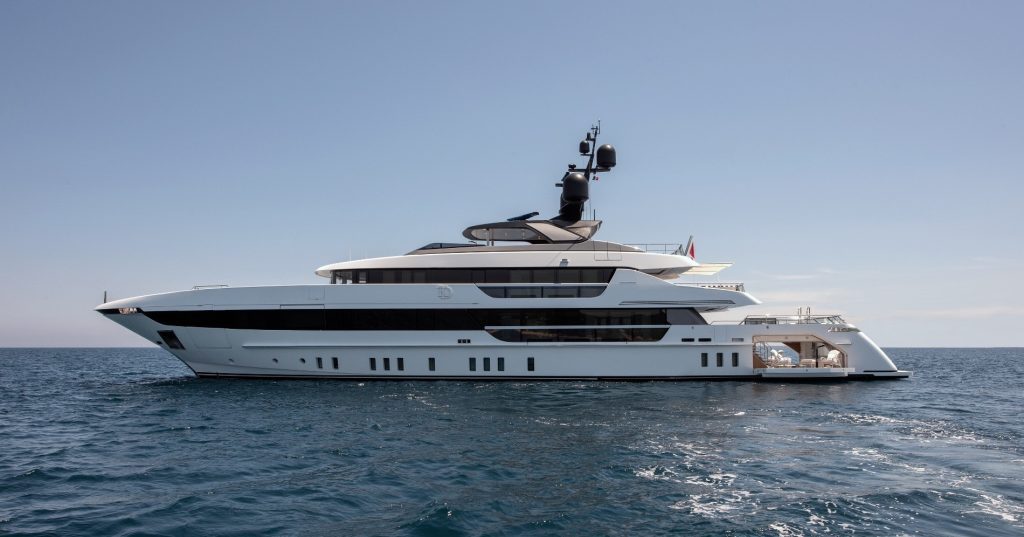
Sanlorenzo Superyacht – 52Steel designed by KYMA Kyma handled nesting documentation, functional diagrams, 3D-engineered model, piping and coordinates, and shipyard assistance.
A bright, efficient future
Two years of using NAPA tools have unlocked new efficiencies and opened new opportunities for KYMA at a time when the company is expanding rapidly, eyeing global markets. “Collaboration with NAPA is excellent, we get precise and timely answers to our questions”, Sergio Allegria highlights.
KYMA is committed to delivering high-quality, safe, efficient and competitive ships. And to achieve this, the company is committed to constantly modernizing its own work processes – using next-generation digital tools to enhance performance at every point. By doing so, KYMA is building the foundations for its innovative, efficient and successful future.