June 17, 2022
Creating flexible designs for sustainable, future-proof vessels
To create the sustainable fleets of the future, key decisions must be made from the very beginning of the design process. This includes creating flexible designs that will enable a ship to incorporate new fuels and technologies throughout its lifecycle, as well as a comprehensive assessment of emissions for each unique design.
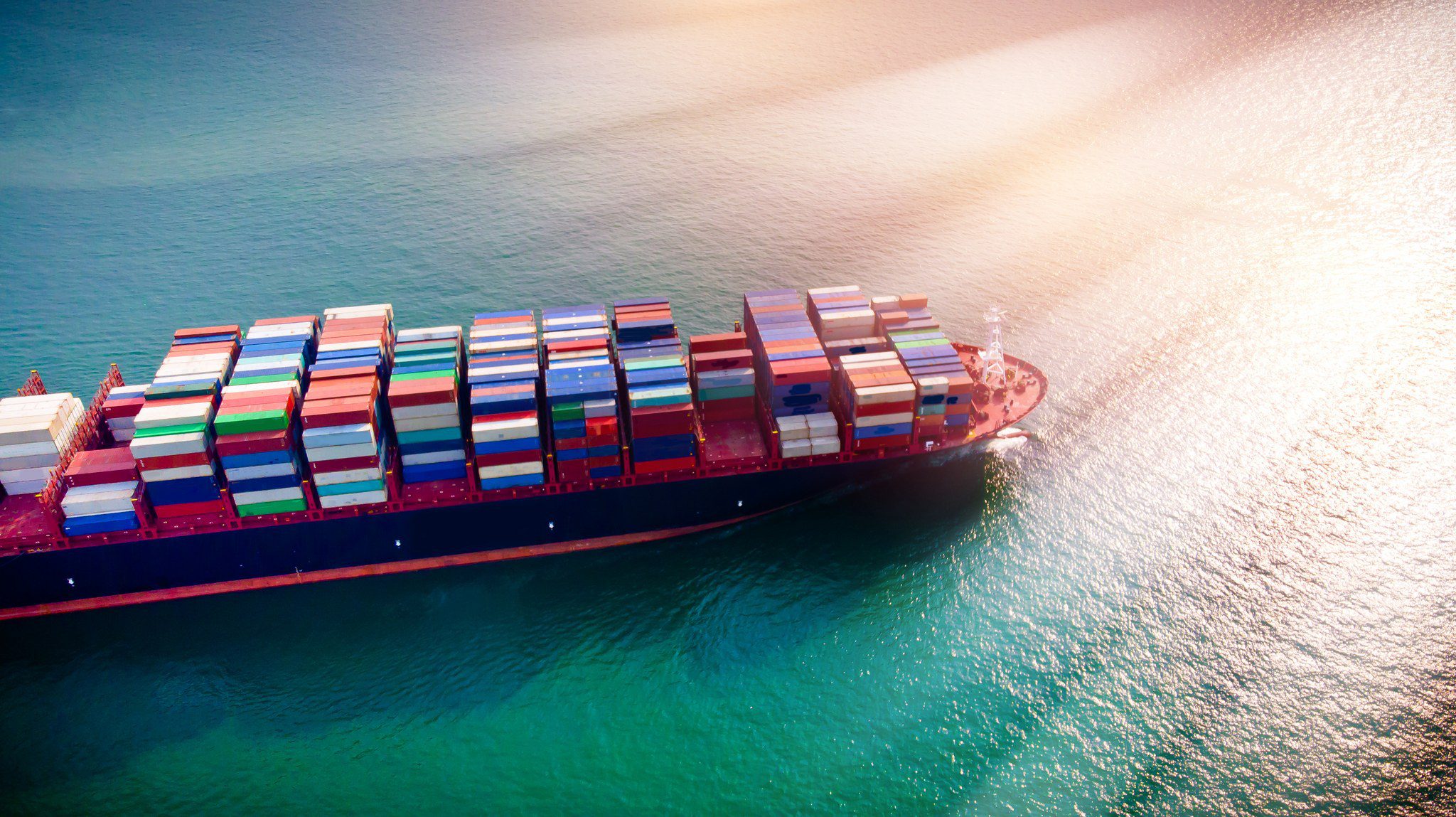
To meet the increasingly stringent decarbonization regulations that will take effect over a ship’s lifetime, the ships designed today need one thing above all: flexibility. There is too much uncertainty about future fuels and new ship power technologies to simply replicate solutions that worked well enough in the past, but might not be flexible enough to still be compliant and competitive in 25 years’ time.
The design decisions that will ensure flexibility – such as allowing for the use of different fuels, new technologies or hybridisation – will make a project more robust in the face of fuel and technology uncertainty. In practice, this might mean allocating more lower deck space to make the installation of alternative fuel tanks easier in the future , or making sure the steel structure will be ready to support the strains of wind propulsion systems, for example.
All these decisions need to be made very early on in a newbuilding project, meaning that the early stages of a design will see frequent, rapid changes. For designers, the key challenge is to balance flexibility against the need for performance and efficiency in the immediate term. To make the right choices, this early stage design process must evolve to involve more dialogue and data exchange between architects, designers, integrators, owners and yards.
The importance of emissions analysis
Ship design is an extremely time-sensitive process, and each design task must produce adequate value in relation to the time spent on it. Meanwhile, in order to build competitive and profitable ships in today’s environment, it is necessary to accurately estimate the individual performance and costs of each new ship – and this must happen early in the design process.
This means that incorporating new clean technologies, such as wind propulsion systems, can be challenging, as in many cases, engineers and designers have no previous experience with these specific technologies. Currently, a plethora of potential ship design options exist that increase fuel efficiency or alter the propulsion system altogether. However, it is difficult to assess these options and compare them to make informed decisions about how to future-proof a ship. Furthermore, for many of these innovative systems, we still have limited data to accurately estimate how these design choices perform in terms of fuel savings and emissions reduction in practice under real operational conditions.

Emissions analysis, then, should become a central part of the design process in the future, increasing as the pressure to decarbonize ramps up. This assessment of future ships’ environmental performance will not be based on a design-focused formula like EEDI, but rather the actual measured fuel consumption which is then converted to CO2 emissions. This fact highlights the need for a data-driven assessment of the expected future operational profiles of the ship, not just an assumed operational point or conditions.
Obtaining accurate, reliable data is complicated by the different conditions faced on different shipping routes. For example, the wind conditions on a cross-ocean voyage may be favourable for some types of kites or sails, but this might not be the case for some short-sea routes.
Making smart decisions from the onset
These emissions assessments should take place in the early design phase, as decisions made at this point will have a fundamental impact on the design as it progresses later. Then again, this phase is the most constrained in terms of how much time can be spent on a single design task, and analysing the true emission levels of a ship is time-consuming and difficult.
Therefore, to enable environmentally-conscious ship design choices, the effort involved in carrying out such analyses must be reduced. Powerful design tools are needed – and, importantly, they need to enable collaboration between all stakeholders.
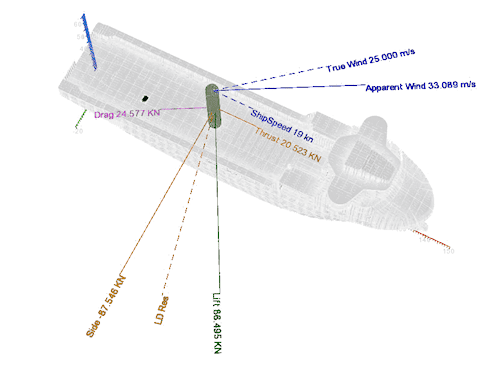
NAPA is uniquely positioned to help. Our design tools are already widely used throughout the industry in the early design phase, and we also possess powerful in-house capabilities in the analysis of operational ship data as well as a large pool of AIS and measured operational data. NAPA’s 3D models enable naval architects and structure engineers to trial-and-error different options in a digital model and optimise each individual design to ensure safety and efficiency. All the information is collated in one system, the NAPA database, which can be accessed by all stakeholders involved in the construction process via tools such as NAPA Viewer, our latest web-based tool to access the real-time 3D model.
We continue to evolve our capabilities, and we are currently researching new ways of incorporating operational data, and information for different decarbonisation technologies into ship designs to achieve the IMO’s decarbonization targets. This will help ensure that the right decisions are made from the early stages of the ship design process, saving precious time and producing a result that will ensure a ship retains its commercial value throughout its lifetime.